In general, when selecting a power supply, it is important to choose one with appropriate voltage and current rating to support the system requirements. Typically, power supplies are connected in parallel to increase the power/current rating and also to increase the system reliability by providing redundancy function. Series connection of power supplies can cater to special needs of the system when requiring higher output voltages.
1. Parallel Operation
The purpose of parallel operation is to get increased output current. When in 1+1 connection, the total output current will be maximum 2x of each individual power supply rating. Load sharing between the 2 supplies can also be achieved. (See “Load Sharing” topic below). When connecting more than one power supply (N+1), it is recommended to connect using external ORing diodes (Delta recommends the use of DRR-20N or DRR-40N). See Figure 2.
To achieve redundancy function, the system current demand should not be greater than the rating of a single power supply. More details are available under the “Redundancy” topic later in this article. In the case of redundant connection, system operation is not disrupted when there is a failure in one of the power supply. This prevents overall system downtime.
Load Sharing Concept
The power supplies can be connected together for parallel operation to increase the output current. See Figure 1 below. To achieve this, it is important that the output voltages of both power supplies must be within 25mV difference of each other. The output voltage adjustment must be done at 50% of max load current or at a load current 25% and above ensuring that both the power supplies have been adjusted at the same current level independently.
Figure 1. Load Sharing Connection Diagram (1+1)
Figure 2. Load Sharing Connection Diagram (N+1)
Redundancy Concept
Power supplies must be connected using ORing diodes to achieve redundant operation. The output voltage difference between the two power supplies is kept typically at 2% of the output voltage. For a 24V power supply, keep a gap of 0.48V (0.45~0.50V). In the event of a failure with one of the power supply, the other power supply will take over the system load. Ensure that the selected power supply is capable of providing the system load (current rating of the power supply must not be lower than system current demand). See Figure 3 below for connection diagram.
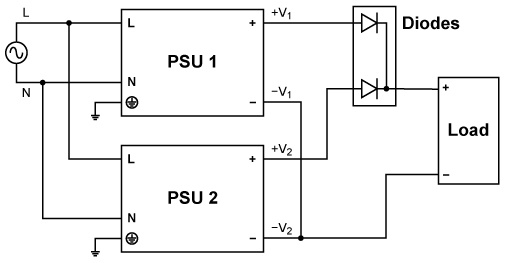
Notes:
The selection criteria for individual ORing diode must be;
- current rating at least 4x of the output load current
- reverse voltage rating 2x of the power supply output voltage
- heat sink with the ORing diode
Increase operational reliability of the system with Delta Redundancy Module
Delta redundancy modules DRR-20N and DRR-40N use Schottky diodes to keep the conduction losses at a minimum. The modules also use potential free contacts to provide an external signal when the failure from either power supply.
Delta recommend the use of DRR-20N and DRR-40N for load sharing and redundant operations. Product details are available via these links DRR-20N and DRR-40N.
Steps to using DRR Module for parallel operation (redundant and load sharing)
Follow the steps below to use DRR-20N and DRR-40N modules.
Step 1: Measure and set output voltage
- For redundant operation;
Measure the output voltages (VO) of PSU 1 and PSU 2. If PSU 1 is the master unit, then VO of PSU 1 must be higher than PSU 2 (0.45~0.50V for 24V or 0.90~1.00V for 48V). To correctly set the output voltage, individually connect each power supply to 50% of the rated load between 85-264Vac input voltage before making the adjustments. - For the load sharing operation;
Measure VO of PSU 1 and PSU 2. The VO difference of PSU 1 and PSU 2 must be within 25mV of each other. To correctly set the output voltage, individually connect each power supply to 50% of the rated load between 85-264Vac input voltage before making the adjustments.
Step 2: Connect power supply units to DRR module
Connect the power supplies PSU 1 and PSU 2 to Vin 1 & Vin 2 of the DRR module. Refer to Figure 4.
Step 3: Connect the system load to Vout
Connect the system load to Vout. Note the output voltage Vout from DRR module = VO (output voltage of power supply) – Vdrop* (DRR module).
*Vdrop will vary from 0.60V to 0.90V (Typical 0.65V) depending on the load current and surrounding air temperature.
**The Signal GND in the DRR module is for the LED and DC OK signals located in the module. The Output GND terminals from the two PSU’s do not need to be connected to the Signal GND terminal.
Figure 4. DRR Module Connection Diagram
**The Signal GND in the DRR module is for the LED and DC OK signals located in the module. The Output GND terminals from the two PSU’s do not need to be connected to the Signal GND terminal.
Figure 4. DRR Module Connection Diagram
2. Series Operation
Power supplies can be connected in series to increase the output voltage as shown in Figure 5. Only power supply from the same product series and with same rated output current should be used.
The maximum load current should not exceed the smallest rated output current, when selecting power supplies with different current ratings. Any number of power supplies can be connected in series. System designers must note that an output voltage > 60Vdc will not meet SELV requirements, and can be dangerous. Under no circumstances the total voltage should exceed 150Vdc. When the total voltage exceeds the SELV limit of 60Vdc, a protective barrier against touching the output terminals must be installed, together with connecting the output ground (-V2 DC Return) terminal of power supply to Earth ground. See Figure 5.
A diode in reverse bias must be added across output terminals of each power supply. This is to prevent -V voltage being applied to other power supply in fault conditions such as short circuit across load. During a short circuit, -V1 & +V1 will be connected across +V2 & -V2 which means the 2 power supplies output will be connected in opposite polarity and will cause damage to the power supplies.
With diode connected in reverse bias across the output, the voltage across each power supply output will be restricted to one diode drop – approximately 0.7V to 1.0V. It is recommended to provide sufficient voltage de-rating for diodes with 2x the voltage rating of series output voltage.
Example: When two 24V power supplies are connected in series, the total voltage will be 48V. During a short circuit, the current through the diodes will be very high. Therefore, use diodes with reverse voltage rating of at least 2 × 48 = 96V.
Figure 5. Series Operation Diagram
Notes:
The selection criteria for individual diode must be;
- current rating at least 2x of the output load current
- Schottky barrier diode with reverse voltage rating 2x of the output load voltage
When two power supplies are connected in series, there is a possibility of a non-monotonic turn ON as the power supply with the fastest startup time and rise time will turn on first. As shown in Figure 6, the combined output voltage waveform of the 2 power supplies connected in series will result in a step.
Figure 6. Non-monotonic Turn-on Waveform
When power supplies are used in parallel and series operations, parameters such as EMI, inrush current, leakage current, PARD, and startup time will be different compared to a standalone power supply. The system designer must consider these parameters on a system level.
For further information please contact one of our Application Engineers or check out our Delta Product range